Sacde, junto con Techint Ingeniería y Construcción, tuvo a su cargo la construcción de los tramos 1 y 2 del gasoducto Néstor Kirchner (GNK). Para cumplir con el objetivo y que el ducto estuviera listo el 20 de junio, trabajaron con equipos de soldadura automática que nunca antes se habían utilizado en el país, lo que agilizó los tiempos y las maniobras de soldado. Si bien los equipos fueron rentados, Sacde decidió adquirir esta nueva tecnología para obras futuras, sobre todo para aquellas que se vinculen al sector del oil & gas, ante el gran desarrollo de Vaca Muerta y los cuellos de botella que existen en materia de infraestructura de transporte. “Durante los últimos años la inversión en nuevos equipos y tecnología fue de US$ 16 millones, pero en el último año se duplicó”, precisó Carlos Coletto, gerente de la Unidad de Negocio de Gas y Petróleo de la compañía.
Sacde incorporó curvadoras, pay welders, biseladoras, acopladores internos, equipos de soldadura automática, tiende tubos hidráulicos y equipos para tapada de tubería con el propósito de mejorar resultados en la construcción, otorgando previsibilidad y aumentando el ritmo de producción de manera sostenida. También, desarrolló la primera escuela de soldadura automática en Argentina en donde se encuentra capacitando a su personal para el uso de las nuevas maquinarias y tecnología.
EconoJournal recorrió el centro de capacitación en donde más de 24 personas de diferentes puntos del país se están formando para convertirse en operadores calificados para los equipos y herramientas requeridos en el proceso de soldadura. Allí, Pablo Brottier, director de comercial de Sacde, comunicó: “Estamos incorporando tecnología para los caños que vienen. Argentina es el lugar en donde hay que estar y producir. La posibilidad que existe es que el país supere el millón de barriles de petróleo y que duplique la producción de gas y para eso se necesita infraestructura”.
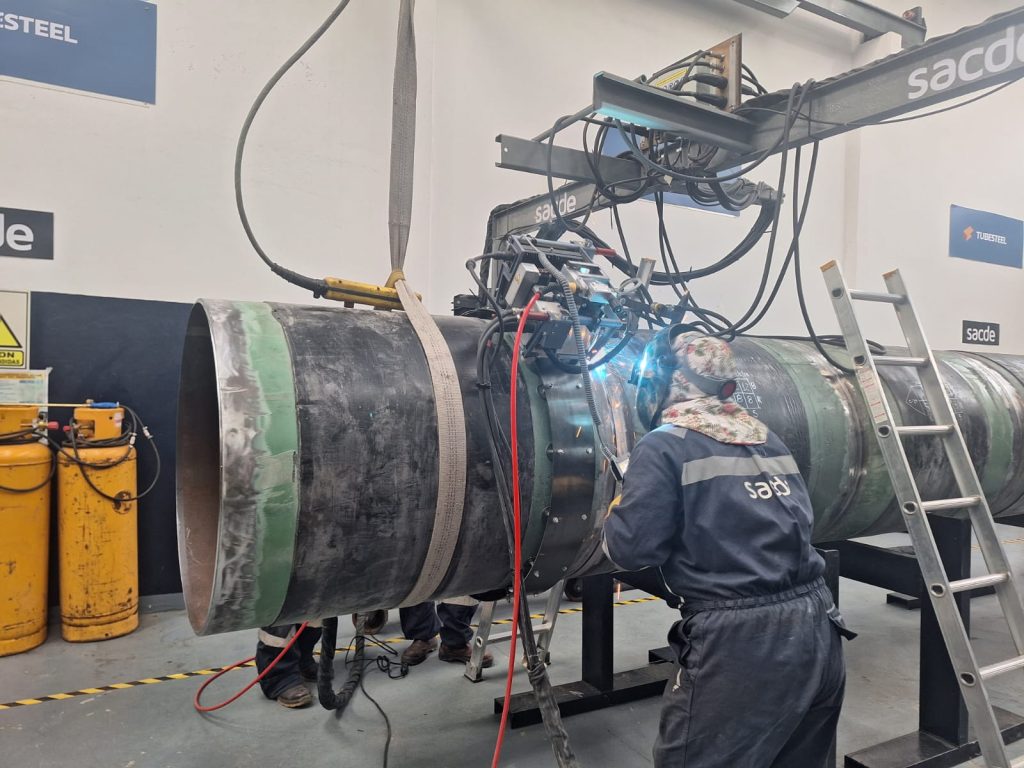
Brottier habló de la oportunidad que tiene la Argentina de exportar hidrocarburos hacia a los países limítrofes como una de las razones que motivaron a la compañía para hacer el desembolso en tecnología. Sobre esto explicó que “necesitamos ductos para exportar gas a los países vecinos y eventualmente para el Gas Natural Licuado. Podemos abastecerlos, pero los ductos que tenemos ahora son insuficientes, hay que hacer más porque los centros de consumo están lejos del recurso”.
Por su parte, Coleto indicó: “Trajimos para el GNK soldadura automática para cumplir con ese gran desafío y lo hemos hecho. Ahora hemos adquirido equipos similares a los utilizados que sirven para caños de diferentes medidas, de 36 y 24 pulgadas”. “Queremos estar a la vanguardia y poner en servicio lo mejor que hay en el mundo para este trabajo. El hombre no se reemplaza, maneja una tecnología diferente”, remarcó.
En ese sentido, compartió: “En 2019 viajé a Europa para analizar estas tecnologías, pero la obra del gasoducto comenzó después. En mayo del año pasado rentamos los equipos en Estados Unidos y llegaron a mitad de octubre y en noviembre compramos los equipos y llegaron en marzo de este año”. Sacde es la única constructora del país que en la actualidad cuenta con este tipo de maquinaria.
Necesidad de infraestructura
Respecto al crecimiento de la producción de Vaca Muerta y su evacuación, Brottier precisó que “si hay que evacuar un millón de barriles, hay que construir 1500 kilómetros de ductos de gran porte, como el GNK. Y si llegamos con el gas hasta Brasil y contamos con el GNL, se necesitarán 3000 kilómetros de gasoductos”.
Aún así advirtió que “existe un mercado de vida corta para el petróleo por la transición energética, pero es una fuente importante de divisas para el país y debemos monetizarla para poder desarrollar el gas que será clave en la transición, por eso nos preparamos comprando la última tecnología”.
Escuela de soldadura
Una de las particularidades que tuvo la construcción del gasoducto Néstor Kirchner fue que el proceso de soldadura contó con un equipo especial de 50 soldadores internacionales, en su mayoría provenientes de Turquía, que contaban con los conocimientos necesarios para realizar esta actividad. Por esta razón y, ante la adquisición de la nueva maquinaria, Sacde desarrolló la escuela de soldadura automática, ubicada en Ciudadela.
“Nos faltaban soldadores, por eso hicimos escuela de soldadura. Necesitamos gente porque esta no es una industria que se automatiza”. “La soldadura automática nos trae eficiencia y da mejores condiciones de trabajo a nuestros trabajadores. Lo que falta para hacer los ductos es capacitación”, contó Maia Chmielewski, directora de Administración y Finanzas de Sacde.
Además Chmielewski, agregó: “Intentamos capacitar para el crecimiento de nuestra compañía y el país. Por eso, también firmamos un acuerdo con la UTN hace dos semanas, y así continuar con este proceso”.
Sobre la participación de los soldadores turcos en el GNK, Coleto explicó que “el país no tenía soldadores para hacer 100 soldaduras por día, por eso necesitamos esa mano de obra”. “En Argentina son muy pocos los supervisores con capacitación técnica. Por eso, hay capacitación continúa, por el objetivo que seguimos a futuro”, indicó.
Bajo esa misma línea, Brottier sumó: “ Damos empleo y empleabilidad. Para que el trabajador tenga el conocimiento en donde sea que se necesite”.
Durante las jornadas de formación se le brindará a los trabajadores 120 horas de capacitación en oficios como soldadura automática, manejo de biseladora automática, presentador y calentador.
Soldadura automática
La soldadura automática otorga más productividad y más seguridad. Los caños obtienen cinco cordones de soldado. La primera vuelta de soldadura demora un tiempo de un minuto y medio y la soldadura completa tarda alrededor de 17 minutos.
Marcelo Bottarini, responsable de la escuela de soldadura, informó que luego de este proceso, “el caño es sometido a un ensayo de ultrasonido para revisar la soldadura y detectar, en caso de que exista, alguna falla. Esto es lo que se hizo en el gasoducto Néstor Kirchner. Es un proceso más confiable y más rápido que las pruebas de pruebas de gammagrafía”.
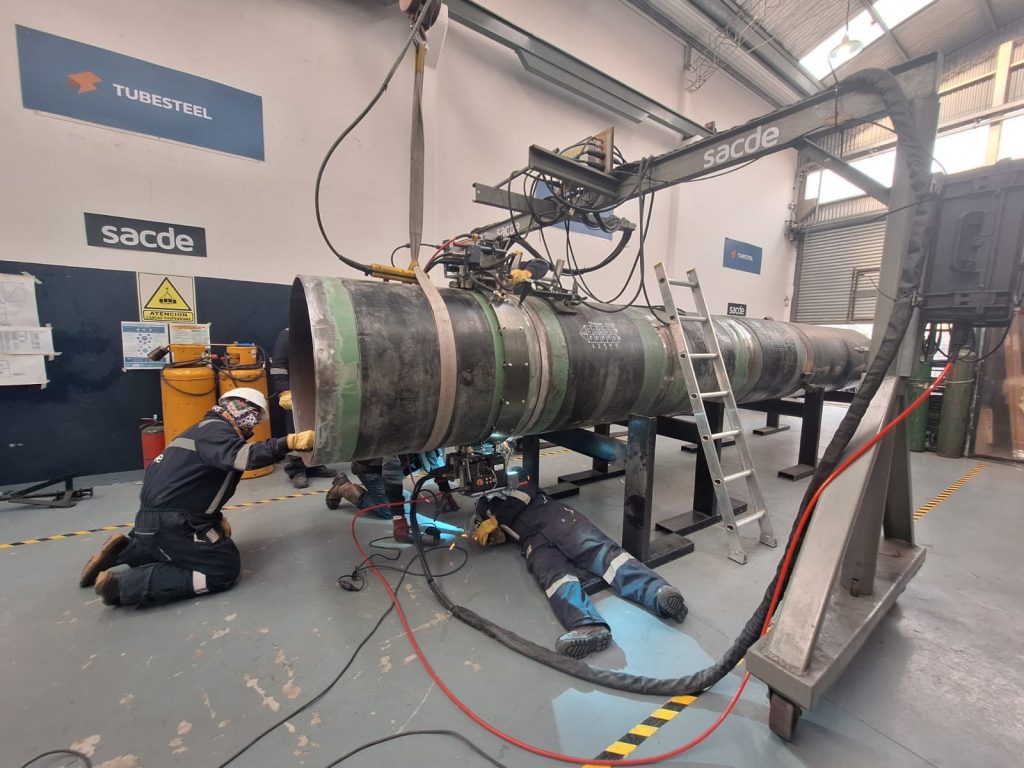
La capacitación surge porque los trabajadores tienen la tarea de programar la máquina, es decir, diagramar la velocidad de la oscilación y el largado del alambre -que es de acero y está recubierto de cobre. La máquina cuenta con un presentador interno, con respaldo de cobre, lo que evita que el calor no pase y que la y que la soldadura quede perfecta, un proceso que es supervisado por los obreros.